What are the Functions of American Standard Oil Casing Tubing?
Date:2022-03-17View:1076Tags:Casing Tubing
Oil casing tubing is the lifeblood of oil well production. In the downhole, in view of the difference in geological conditions, the downhole stress conditions are complex, and the comprehensive effects of tension, compression, bending, and torsion have raised the requirements for the quality of the casing itself. Therefore, the functional requirements of American Standard tubing depend on the application. According to the applicable situation, it can be divided into diversion pipe, surface pipe, technical pipe and oil layer casing. Welded steel pipes are divided into two ordinary wall thicknesses: ordinary oil jacket and thick oil jacket.
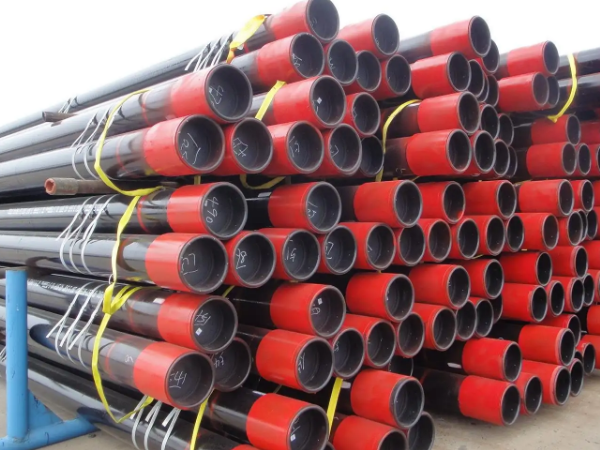
Different types of American standard oil casings are used in the oil production process: for the purpose of maintaining drilling, to avoid contamination of shallow and shallow gas layers, to support wellhead devices, and to bond the weight of other layers of casing; technical casings will be of different grades The pressure is separated to ensure the normal flow of drilling fluid quantitatively; the manufactured casing is maintained. Install crack guards, leak guards and liner for maintenance drilling and stratified drilling fluid drilling rigs. The oil pipe should have properties such as corrosion resistance and corrosion resistance. In the case of complex geological conditions, the oil pipe should have anti-collapse and anti-microbial erosion effects. With the vigorous development of the oil industry, the direct buried pipes, American standard oil casings and tank bottoms of oilfields are seriously corroded, especially American standard oil casings, which seriously affect the production, development, design and surrounding environment of oilfields. There is corrosion on the inner and outer walls of oil and gas wells, and the internal corrosion is more serious.
Anti-corrosion measures for American standard tubing:
1) To do a good job of qualified water quality and strict water quality inspection and supervision. Implement the drainage system, strengthen the cleaning of the main pipeline, ensure that the quality of the station and bottom water meets the requirements, and reduce the import of non-staple food sources.
2) For new injection wells, select sterilization-based circulating protection fluid, and establish a system to add it in time.
3) Considering the accelerated effect of mechanical wear on the corrosion of the oil casing, it is recommended to add a rubber ring to the oil pipe joint, or add an aggregate device to the offset part to prevent the pipe wall and side from contacting the casing during operation and water injection. At that time, the bacteria are seriously corroded, and the sulfate-reducing bacteria grow slowly after high temperature removal. You can add 100°C warm water or steam to the reflux hole in time, and the sulfate-reducing bacteria can be removed at this time.
4) Unless the water injection well casing corrosion is reasonably and effectively controlled, cathodic protection and coating casing should not be promoted.