What is the Manufacturing Process of Square Tube?
Date:2022-05-16View:1721Tags:Square Tube, Manufacturing Process
The square tube is rolled from strip steel through process treatment. Generally, the strip is unpacked, flattened, coiled, welded to form a round tube, and then rolled into a square tube from the round tube and then cut to the required length.
1. The definition of carbon steel is that the iron-carbon alloy with five elements in the steel containing less than 2% carbon is called steel. The five elements in carbon steel refer to the main components in the chemical composition, namely C, Si, Mn, S, P; secondly, gas is inevitably mixed in the steelmaking process, including O, H, N; in addition , In the aluminum-silicon deoxidation process, Al must be contained in the molten steel. When Als (acid-soluble aluminum) ≥ 0.02%, it also has the effect of refining grains.
According to the production process, the square tube is divided into: hot-rolled seamless square tube, cold-drawn seamless square tube, extruded seamless square tube, and welded square tube. Among them, the welded square pipe is divided into: straight seam welded square pipe, spiral welded square pipe, etc.
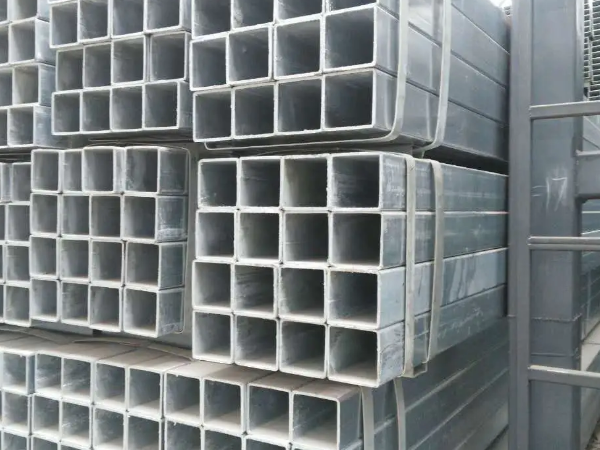
2. The main task of steelmaking is to adjust the content of carbon and alloying elements in the steel to within the specified range according to the quality requirements of the steel being made, and to reduce the content of impurities such as P, S, H, O, N to the allowable limit under. The steelmaking process is essentially an oxidation process. The excess carbon in the charge is oxidized and burned into CO gas to escape, and other Si, P, Mn, etc. are oxidized and enter the slag. Part of S enters the slag, and part of it generates SO2 and is discharged. When the composition and temperature of molten steel meet the technological requirements, the steel can be tapped. In order to remove excess oxygen in the steel and adjust the chemical composition, deoxidizers and iron alloys or alloying elements can be added.
3. The blooming die cast steel ingot adopts the new process of hot charging and hot delivery, enters the soaking furnace for heating, and then is rolled into the blooming products such as slab, tube billet, billet, etc. through the blooming mill and the continuous billet rolling mill. , cutting tail, surface cleaning (flame cleaning, grinding), high-quality products need to be peeled and flawed on the bloom, and put into storage after passing the inspection. At present, the products of the blooming plant include blooming slabs, rolled billets, steel billets for oxygen cylinders, round tube billets for gears, axle billets for railway vehicles and steel for plastic molds.
4. Converter steelmaking: The molten iron transported from the truck can be poured into the converter as the main charge after desulfurization, slag blocking, etc., plus less than 10% of scrap steel. Then, blow oxygen into the converter for combustion, the excess carbon in the molten iron is oxidized and a lot of heat is released. When the probe reaches the predetermined low carbon content, the oxygen blowing is stopped and the steel is tapped. Generally, deoxidation and adjustment of components are required in the ladle, and then carbonized rice husks are thrown on the surface of the molten steel to prevent the molten steel from being oxidized, and then it can be sent to the continuous casting or die casting area. For high-demand steel grades, bottom blowing argon, RH vacuum treatment, and powder spraying (spraying SI-CA powder and modified lime) can be added, which can effectively reduce the gas and inclusions in the steel, and further reduce carbon and sulfur. After these out-of-furnace refining measures, the composition can be fine-tuned to meet the needs of steel such as seamless square tubes.